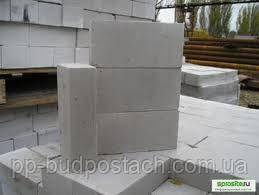
Производство блоков из газосиликата.
Блоки из газосиликата – это широко распространенный строительный материал, который относится к ячеистым бетонам, производится в виде искусственного пористого камня с применением метода автоклавной обработки и обладает существенно более низкой плотностью и теплопроводностью по сравнению с тяжелыми бетонами.
Сегодня существует большое количество производственных площадок, которые изготавливают автоклавные ячеисто-бетонные блоки (газосиликат). Все они применяют, по сути своей, единую базовую технологию, которая была запатентована еще в 1924 году шведским архитектором по имени Аксель Эрикссон.
Первая стадия производства газосиликатных блоков включает в себя процесс создания рабочей смеси из портландцемента, кварцевого песка, негашеной извести и воды. Раствор тщательно перемешивается, после чего в него подается алюминиевая паста или порошок. Тщательно перемешанная бетонная смесь заливается в специальные металлические формы, в которых выстаивается в течение нескольких часов. В это время происходит вспучивание бетона, чему способствует естественная химическая реакция между алюминием и известью. В структуре бетона образуются характерные для ячеистых бетонов мелкие поры. После этого газосиликат отправляется на линию точной резки, где разрезается на блоки тонкими и прочными стальными струнами толщиной до одного миллиметра.
Теплоизоляционно-конструкционные блоки из газосиликата применяются не только в качестве утеплителя, но также и для возведения несущих стен одноэтажных домов и других зданий. К этой категории можно отнести блоки марки D500.
Готовые газосиликатные блоки помещаются в автоклав, который представляет собой специальную установку для повышения эффективности реакции с помощью высокой температуры и повышенного давления. В течение 12 часов блоки из газосиликата проходят автоклавную обработку при температуре +190 градусов по Цельсию и под давлением, примерно, 12бар. Автоклавная обработка призвана усилить реакцию между известью и алюминием, которые полностью распадаются, образуя чистый водород. Сферические поры равномерно распределяются по всей структуре газобетонных блоков.
Виды блоков из газосиликата
Теоретически можно разделять газосиликатные блоки и газобетонные. Разница между ними заключается в использовании разных вяжущих элементов. Газосиликат производится на основе известковых вяжущих компонентов, а газобетон – на основе цемента. Однако на современном строительном рынке блоки из чистого газосиликата (только на основе извести) и чистого газобетона (только на основе цемента) встретить практически невозможно. Все современные производства используют для изготовления газосиликатных блоков смесь вяжущих, то есть и известь, и цемент в различных соотношениях. Поэтому на практике термины «газосиликат» и «газобетон» стали словами-синонимами, обозначающими, по сути, один и тот же вид блоков из автоклавного ячеистого бетона.
Блоки из газосиликата внешне и по структуре схожи с пенобетоном, который также относится к ячеистым бетонам, но только неавтоклавного твердения. Качественный пенобетон внешне можно легко перепутать с газосиликатом. Однако они имеют разные физические характеристики. Пенобетон, обладая одной и той же плотностью с газосиликатом, будет иметь несколько более тяжелый вес и больший коэффициент теплопроводности. К тому же по показателю прочности пенобетон совершенно не может конкурировать с газосиликатом, поэтому сферой применения пенобетона является теплоизоляция зданий, возведение внутренних перегородок и закладка проемов. Поры в газосиликатном блоке носят открытый характер, у пенобетона они отделены друг от друга, поэтому он легко может держать на поверхности воды. В связи с этим стоит отметить, что не рекомендуется вести строительство из газосиликатных блоков в среде с влажностью выше 60%.
Применение блоков из газосиликата
По типу применения блоки из газосиликата разделяются на три группы: теплоизоляционные, конструкционные и теплоизоляционно-конструкционные.
Теплоизоляционные блоки из газосиликата используются для утепления зданий, возведения ненесущих стен и перегородок, а также для закладки проемов. Примером такого типа материала могли бы послужить газосиликатные блоки марок D100, В 200 и D 300. Однако они сегодня практически не производятся. Если блоки D400 можно встретить повсеместно, то D300 уже редкость, так как серьезные производители не считают рентабельным изготавливать газобетонные блоки такой низкой плотности. В связи с этим к ряду теплоизоляционных блоков можно отнести марку D400. Хотя некоторыми индивидуальными застройщиками она все же применяется для возведения несущих стен при строительстве одноэтажных зданий. Хотя из-за небольшого показателя прочности газосиликатных блоков D400 возводить из них несущие конструкции не рекомендуется. Для этого существуют газобетонные блоки с более высокими характеристиками прочности.
Теплоизоляционно-конструкционные блоки из газосиликата применяются не только в качестве утеплителя, но также и для возведения несущих стен одноэтажных домов и других зданий. К этой категории можно отнести блоки марки D500, которые имеют прочность при сжатии 40,7 кгс/см2 – у блоков Ytong и 35 кгс/см2 – у большинства других известных производителей, теплопроводность 0,99 Вт/мС – у блоков Ytong и 0,12 Вт/мС у остальных производителей.
Конструкционными считаются газосиликатные блоки всех марок, начиная от D1000. Однако на практике можно редко встретить газосиликат плотностью выше, чем D800. Поэтому фактически в качестве конструкционного строительного материала сегодня применяются любые более высокие марки газосиликатных блоков, начиная с D600. Конструкционные блоки газосиликата предназначены для возведения несущих стен при строительстве домов и других зданий высотой выше трех этажей. Более высокая плотность газобетона обеспечивает и более высокие показатели прочности, однако немного повышает и коэффициент теплопроводности. Таким образом, блоки марки D600 имеют прочность 35-45 кгс/см2 и теплопроводность 0,14 Вт/м`С.
Сегодня газосиликатные блоки активно используются в малоэтажном строительстве. Свою широкую популярность они получили благодаря своей низкой теплопроводности, показатели которой уступают только характеристикам такого материала, как дерево. Но в отличие от дерева, блоки из газосиликата огнеустойчивы, обладают большим запасом прочности, не поддаются заражению грибков, плесени и других вредных микроорганизмов.
Рекомендации по отделке ячеистобетонных стен жилых и промышленных зданий.
НИИЖБ Госстроя СССР
Рекомендации по отделке ячеистобетонных стен жилых и промышленных зданий.
Москва 1987 г.
Предисловие
Автоклавные ячеистые бетоны (газо- и пенобетоны, газо- и пеносиликаты, газосиликаты и другие разновидности) являются эффективным материалом для наружных стен жилых, общественных и производственных зданий. Они имеют небольшую плотность (700-600 кг/м3),высокие технические свойства и прочность (М50-М25), достаточную для применения их в виде армированных стеновых панелей в многоэтажных зданиях. Следовательно, применение стен из ячеистых бетонов является перспективным. Однако, вследствие повышенной пористости ячеистых бетонов, стены из них должны иметь более надежную, чем обычно, отделку как наружных, так и внутренних поверхностей. Такие способы отбелки были подобраны, применены и проверены многими организациями на протяжении тридцатилетнего опыта отечественного домостроения со стенами их ячеистых бетонов. Общие данные об основных рекомендуемых способах отделки приведены в действующей «Инструкции по изготовлению изделии из ячеистого бетона» (СН 277-80). Настоящие Рекомендации содержат более подробные производственные дополнения, необходимые для осуществления рекомендуемых способов отделки, как на заводах, так и в построечных условиях. Кроме того, в них включены некоторые новые способы отделки, а также приведены рекомендации по отделке стен из мелких блоков. Рекомендации разработаны НИИЖБ Госстроя СССР (арх. Т.В. Косточкиной, инж. Т.А. Щербаковой, канд. техн. наук В. В. Макаричевым при участии инженеров О.И. Марголиной и В. М. Хохраковой). При составлении Рекомендаций использованы материалы ВНИИСТРОМа им. П.П. Будникова и НИПИСиликатобетона Минстройматериалов СССР, НИИ по строительству Госстроя ЭССР, ЛатНИИ строительства Госстроя , ЛатССР Каунасского НИИСиА Госстроя ЛитССР и Уралпромстройниипроекта Госстроя СССР. Все замечания и предложения по настоящим Рекомендациям просим направлять в НИИЖБ Госстроя СССР по адресу: 109389, Москва, 2-я Институтская ул., д. 6.
Дирекция НИИЖБ
1. Общие положения.
1.1. Настоящие рекомендации распространяются на отделку наружных поверхностей стеновых панелей их автоклавных ячеистых бетонов, осуществляемую в заводский условиях, и на отделку наружных поверхностей стен зданий из панелей и мелких блоков, выполняемую в построечных условиях.
1.2. Отделка панелей в заводских условиях подразделяется на отделку, осуществляемую в процессе формования панелей (т. е. до автоклавной обработки), и отделку, осуществляемую после распалубки (т.е. после автоклавной обработки) на специальных постах или конвейерных линиях.
1.3. Для отделок, осуществляемых в процессе формования панелей, используются коврово-мозаичные плиточные материалы, каменные дробленые материалы и декоративные поризованные растворы. Краткие характеристики видов отделок и основные исходные материалы:
ВИД ОТДЕЛКИ ОСНОВНЫЕ МАТЕРИАЛЫ КРАТКАЯ ХАРАКТЕРИСТИКА
Коврово-мозаичными плиточными материалами Коврово-мозаичная стеклянная плитка. Коврово-мозаичная керамическая плитка. Коврово-мозаичная керамическая плитка типа «брекчия». Отделка производится путем раскладки ковров с плиткой на дне формы с последующей укладкой промежуточного слоя из поризованного раствора и заливкой ячеистобетонной смеси. Поризованные растворы могут быть цветными. Фактура отделочного слоя гладкая (см. пп. 4.13 - 4.17)
Каменными дроблеными материалами Дробленый гранит, мрамор и другие горные породы фракции 10-20, 20-30 мм. Отделку производят путем раскладке на дне формы каменных дробленых материалов на слой песка или на слой саморазрушающегося клея. Фактура отделочного слоя «под шубу» (см. пп. 4.7 -4.12)
Декоративными поризоваными растворами Цветные цементно-песчаные растворы с воздухововлекающими или пенообразующими добавками. Рельефообразующие материалы. Отделку производят путем укладки на дно формы слоя поризованного раствора толщиной 2-3 см. Фактура отделочного слоя гладкая или рельефная (см. пп. 4.2 -4.6).
1.4. Для отделок, осуществляемых в заводский условиях после распалубки панелей, используют различные краски, эмали, декоративные мелкозернистые присыпки и комбинированные гидрофобные составы. Основные исходные материалы и краткие характеристики различных отделок, осуществляемых после распалубки панелей:
ВИД ОТДЕЛКИ ОСНОВНЫЕ МАТЕРИАЛЫ КРАТКАЯ ХАРАКТЕРИСТИКА
Краски водоэмульсионные Водоэмульсионные краски Э-КЧ-112 и Э-ВА-17 Краски цветные, постельных тонов, растворяются водой. Выпускаются лакокрасочными заводами. Фактура - гладкая, шероховатая. Наносятся в 23 слоя на сухую поверхность при t = 5-8 0С (см. пп. 5.15 - 5.16)
Краски поливинилацетатные ПВАЦ, ПВАГ, латексно-цементные Дисперсия ПВА латекс СКС - 65 ГП, наполнители Краски готовят на предприятиях ячеистого бетона. Фактура - гладкая, шероховатая. Введение в краску пигментов позволяет получить отделочные покрытия широкой цветовой гаммы. Наносятся в 2-3 слоя на сухую поверхность. Время сушки покрытия 2-3 часа в естественных условиях и 40-60 минут при t = 60-80 0С (см. пп. 5.17 - 5.18)
Краски на органических растворителях Краски органические на растворителях ЦПХВ, ОМС ВН-30 ДТС, ХП-71ф марки К. Краски на растворителях. Выпускаются лакокрасочными заводами в готовом виде. Цветные, пастельных тонов. Фактура - гладкая. Окраска выполняется на постах, оборудованных приточно-вытяжной вентиляцией. Наносятся в 2-3 слоя при t не ниже 5 0С. Время формирования покрытия 2,5 ч (см. пп. 5.22 и 5.24).
Краска органическая «Сикра -1» Лак ХВ-784, растворитель Р-4, наполнители Могут изготавливаться на предприятиях ячеистого бетона. Фактура шероховатая. Окраска выполняется на постах, оборудованных приточно-вытяжной вентиляцией. Наносятся в 2-3 слоя при t не ниже 5 0С. Время высыхания покрытия 1,5-2 ч. (см. п. 5.28).
Краски цементные с добавкой ПВА Цемент белый, известь, дисперсия ПВА, цветной пигмент и др. Цементные краски приготавливаются (перед употреблением) путем перемешивания сухих компонентов с водой (см. п. 5.19).
Эмали Эмаль КО-174 на органическом растворителе Выпускаются лакокрасочными заводами в широкой цветовой гамме. Фактура - гладкая. Наносятся в 2-3 слоя при t = 5 0С. Время формирования покрытия 2,5 ч. Отделка выполняется на постах, оборудованных приточно-вытяжной вентиляцией (см. п. 5.25).
Полимерминеральные растворы («Полифос» и «Полигран») Фосфогипс, дисперсия ПВА, латекс, каменная, керамическая или ячеистобетонная крошка крупностью 1-3 мм и др. Составы готовят на предприятиях ячеистого бетона или строительной площадке. Фактура -гладкая, шероховатая. Наносят в 2-3 слоя толщиной 2-3 мм при t не ниже 5 0С. Время формирования покрытия при 18-20 0С 3-4 ч. Рекомендуется для отделки на стадии строительства (см. пп. 5.20 - 5.21).
Декоративные присыпки по клеящему основанию Дробленые каменные материалы, стеклобой, керамзитовый песок и др., фракции до 5 мм. Клеящие составы: «Декор», АЦС, ПВАЦ, ПВАГ, «Полифос», лак Э-ВА-5189 Декоративную присыпку получают со стекольных заводов, клеящие составы готовят на предприятиях ячеистого бетона. Фактура -шероховатая. Последовательно наносят клей, декоративная присыпка, закрепляющее покрытие (или без него). Рекомендуется для отделки зданий в заводских условиях на механизированных линиях или на стендах (см. пп. 5.30 - 5.34).
Гидрофобные комбинированные краски Кремнийорганические гидрофобные жидкости Сначала на панели наносят гидрофобные составы, а ГКЖ-10, ГКЖ-11, краски ПХВ, ХСПЭ и другие, растворители затем различные разновидности красок (см. пп. 5.26 - 5.27).
Тонкослойные штукатурки (декоративные растворы) Дисперсия ПВА, эмульсия МБМ-5с, латекс СКС-65ГП, цемент, песок, пигмент. Приготавливаются на предприятиях ячеистого бетона. Наносятся в 3 слоя. Фактура гладкая, шероховатая (см. п. 5.34).
1.5. Отделка должна быть указана в соответствующих чертежах проектов зданий, согласована с заказчиком, с предприятием-изготовителем стеновых панелей или с организацией, осуществляющей строительство зданий со стенами из мелких блоков.
1.6. Изготовление стеновых панелей и мелких блоков осуществляется в соответствии с «Инструкцией по изготовлению изделий из ячеистого бетона» СН 277-80.
1.7. Качество изделий должно соответствовать требованиям действующих ГОСТов: ^ на стеновые панели жилых зданий - ГОСТ 11024-84; > на мелкие стеновые блоки - ГОСТ 21520-76.
1.8. В районах строительства с сухим и нормальным климатом можно применить все рекомендуемые виды наружных отделок без дополнительных мер по защите поверхности от увлажнения. В районах, отличающихся большим количеством выпадающих осадков (дождей) рекомендуется наносить на законченные отделки бесцветные дополнительные гидрофобные покрытия.
1.9. В условиях севера в качестве основных видов отделки рекомендуется окраска составами на органических растворителях (светлых, теплых тонов), офактуривание поризованными растворами с каменными или плиточными материалами, либо с рельефно поверхностью.
2. Требования к отделке.
2.1. Отделка по своим физико-техническим и основным эксплуатационным свойствам должна удовлетворять требованиям:
ФИЗИКО-ТЕХНИЧЕСКИЕ СВОЙСТВА МЕТОД ОПРЕДЕЛЕНИЯ ТРЕБУЕМЫЕ ЗНАЧЕНИЯ
Сопротивление паропроницанию По диффузии насыщенного водяного пара через образец ячеистого бетона с отделочным слоем в среду ненасыщенного при относительной влажности воздуха ф=50 % Rn < 4 м2 ч мм рт. ст/г
Водопроницаемость отделочного слоя По капиллярному водопоглощению в течение 24 ч слоя бетона толщиной 3 см за отделочным покрытием Wo6 < 5% или w = 2,5 кг/м2
Адгезия к ячеистому бетону Испытанием на отрыв отделочного слоя после 14 сут. хранения при t = 18-20 0С и ф = 50-60 % Ясц > 0,6 МПа
Устойчивость к разрыву По растяжению покрытия при изгибе до образования трещины 0,3 мм
Эксплуатационная стойкость При комплексном воздействии атмосферных факторов w < 5% сохранение первоначального внешнего вида Якон = 0,75
Морозостойкость По ГОСТ 12852.4 - 77 После 35 циклов сохранение первоначального внешнего вида и Ясцкон = 0,75 ЯСц нач
Плотность поризованного раствора марки 75-100 По ГОСТ 12852 - 67 с изм. 1200 - 1400 кг/м3
Модуль упругости поризованного раствора Е п.р. < 3,5 Е яч. бет.
2.2. Внешний вид отделки должен соответствовать эталону, согласованному предприятием - изготовителем с заказчиком.
2.3. При отделке панелей в процессе их формирования каменными дроблеными материалами толщина отделочного слоя не должна превышать 40 мм.
2.4. В промышленных районах с повышенной запыленностью окружающей среды не рекомендуется применять для отделки декоративные присыпки, облицовочные материалы (стеклянные и керамические плитки), асбестоцементные листы, плиты из естественного камня и др.
3. Основные материалы.
3.1. Для отделки поверхностей изделий применяют следующие основные материалы: минеральные вяжущие, полимерные связующие, лаки, краски, эмали, наполнители, дробленые материалы, декоративные присыпки, облицовочные материалы (стеклянные и керамические плитки), асбестоцементные листы, плиты из естественного камня и др.
Минеральные вяжущие:
> цемент белый, цветной и серый мари не ниже М300 (ГОСТ 965 - 78; ГОСТ 15852 - 82; ГОСТ 10178 - 76 с изм.);
> • известь-кипелька и известь пушонка (ГОСТ 9179 - 77) с содержанием негидратированных частиц оксида кальция и оксида магния не более 1%, скорость гашения не менее 5 или не более 25 мин, с удельной поверхностью около 2500 см2/г;
> • известкого-песчаная смесь активностью35-40% и с удельной поверхностью не менее 4500 см2/г.
Полимерные связующие:
> акриловая эмульсия МБМ-5с (ТУ 6-01-274-74);
> • синтетические бутадиен-стирольные латексы СКС-65 ГП, СКС-60ГП и СКС-65ГП «Б» (ГОСТ 10564 - 75 с изм.);
> • поливинилацетатная 50%-я пластифицированная дисперсия ПВА марок ДБ-47/7 и ДБ-40/2с (ГОСТ 18992 - 80 с изм.);
> эпоксидная смола ЭД-5 и ЭД-6 (ГОСТ 10587 - 84);
> лак Э-ВА-5189 (ТУ 6-10-17-47-80);
> клей казеиновый (ГОСТ 3056 - 74 с изм.);
> дисперсия С-135 и СВЭД-10 (ТУ6-10-10079-70, ТУ 6-05-041-399-72). Плиточные материалы:
> керамическая плитка (неглазурованная и глазурованная) размером 48*48 мм со швом не менее 7 мм и плитка «брекчия» (ГОСТ 17657 -79, ГОСТ 13996 - 84); ^ коврово-мозаичная стеклянная плитка размером 21*21 мм со швом не менее 4 мм ± 1 мм (ГОСТ 17057 - 80).
Дробленые материалы:
> • каменные, стеклобой, отходы керамической плитки и другие естественные и искусственные материалы крупностью 10-20; 20-40 мм для отделки изделий в процессе их формирования и 1,2-1,6; 1,7-2; 2,1-2,5; 2,6-5 мм для отделки декоративной присыпкой. Применять дробленые материалы для присыпки в виде смеси различных фракций не рекомендуется;
> естественные каменные материалы - гравий, мрамор, доломит, плотный известняк и другие должны удовлетворять требованиям ГОСТ 22756 - 77 с изм. И ГОСТ 8268 - 82;
> • искусственные материалы - эрклез, битое стекло и отходы стеклоплитки, бой кирпича, отходы форфоро - фаянсовой промышленности, грануляты (газобетонной, керамической, керамзитовой и др.), выдерживающие не менее 35 циклов попеременного замораживания и оттаивания. Краски водоэмульсионные:
> стирол - бутадиеновые Э-КЧ-112 (ГОСТ 19214-80);
> • поливинилацетатные Э-ВА-17 (гост 20833 - 75 с изм.).
Краски, лаки и эмали на органических растворителях:
> • кремнийорганические эмали КО-174 различных цветов ТУ 6-02-57675)
> органосиликатная краска ОМС ВН-30 ДТС (ТУ 84-725-78);
> лак КО-85 (ГОСТ 11066 - 74)
^ хлорсульфированный полиэтиленовый лак ХП-734 (ТУ 6-02-115284);
> • полихлоридный лак ХВ-784 (гост 7313 - 75 с изм.);
> алкидный лак ПФ-060 (ТУ 6-10-612-74);
> перхлорвиниловый лак (СТУ 30-21040-63).
Наполнители:
> • песок кварцевый (ГОСТ 8736 - 77 с изм.) с модулем крупности 1,5-2 для поризованных растворов, с модулем крупности 2-2,5 и влажностью 5-6% без комков, гравия, гальки для подстилающего слоя при отделке каменными дроблеными материалами, молотый -до удельной поверхности 2000-3000 см2/г для клеевых составов;
^ фосфогипс - отход производства экстракционной кислоты с содержанием САБО 2Н2О - 90-95%.
Добавки:
пенообразователь ПО-6;
смола нейтрализованная воздухововлекающая обиетиновая СНВ (ТУ 81-05-75-69);
углекислый натрий (ГОСТ 2156 - 76 с изм.);
кремнефтористый натрий;
дибутилфталат (ГОСТ 6102 - 78 с изм.);
полиэтиленполиамин (ТУ 6-02-594-70);
порошок стиральный (ГОСТ 6-15-1012-76);
железо сернокислое (ГОСТ 4148 - 78);
сульфонол (ТУ 8-373-72);
КМЦ (ГОСТ 6-05-386-80);
жидкое стекло (ГОСТ 13078 - 81);
тальк технический (ГОСТ 19729 - 74).
Гидрофобизирующие жидкости:
> ГКЖ-10 (ГОСТ 13032 - 77 с изм.);
> ГКЖ-11 (ГОСТ 13004 - 77 с изм.);
> жидкость 136-41 (ГОСТ 10894 - 76 с изм.);
> жидкость КЭ-30-04 (ТУ 6-02-816-78).
Растворители:
> Р-4 (ГОСТ 14710 - 78 с изм);
> Р-5 (ТУ МХП 2191 - 50);
> ксилол (ГОСТ 9949 - 76 с изм.);
> толуол (ГОСТ 5789 - 78 с изм.);
> уайт - спирит (ГОСТ 3134 - 78 с изм.);
> керосин (ГОСТ 4756 - 77).
3.2. Перед употреблением должна производится контрольная проверка соответствия сырьевых материалов требованиям государственных стандартов и дополнительным требованиям настоящих Рекомендаций.
3.3. Хранение материалов должно осуществляться в условиях, исключающих возможность их увлажнения, загрязнения и смешивания.
4. Технология отделки, осуществляемой в процессе формования панелей.
4.1. Отделка наружных поверхностей в процессе формования панелей в горизонтальных формах осуществляется путем укладки на дно формы слоев из обычных или цветных поризованных растворов или слоев из каменных и плиточных материалов с последующей заливкой ячеистобетонной смесью, т.е. по способу формования «лицом вниз». При отделке плиточными или каменными дроблеными материалами по литьевому способу формования (без применения вибрации) перед заливкой ячеистобетонной смеси по этим материалам укладывается промежуточный слой из поризованного раствора толщиной 2 см.
4.2. Поризованные растворы приготавливают перемешиванием с водой портландцемента или смешанного вяжущего, заполнителей и воздухововлекающих или парообразующих добавок. В качестве порообразователя рекомендуется применять добавку СНВ, а также комплексные добавки пенообразователя ПО-6 с сернокислым железом в воде 15 %-го водного раствора в количестве 30 % массы ПО-6 или сульфонола с жидким стеклом в соотношении сульфонол: жидкое стекло 1 : 3 по массе.
4.3. Декоративные качества поризованного раствора достигаются введением в его состав цветных цементов или минеральных пигментов в количестве 0,5-5% массы цемента.
4.4. Поризованные растворы приготавливаются в смесителях принудительного действия с числом оборотов не менее 80 и не более 150 в мин. Сначала в смеситель вводят воду и добавки (кроме сульфонола, который вводится в виде порошка после загрузки всех компонентов) и перемешивают в течении 2 мин, затем в смеситель загружают вяжущие, заполнитель и перемешивают 5-10 мин. Продолжительность перемешивания определяется временем необходимым для получения раствора требуемой плотности.
4.5. Дозирование сухих компонентов смесей при приготовлении поризованных растворов производят по массе с точностью ± 2% для вяжущих, ± 3% для заполнителей. Вода и пенообразующие добавки дозируются по объему.
4.6. Поризованный раствор укладывают на дно формы равномерным слоем толщиной около 2 см. При этом консистенция раствора должна быть такой, чтобы после укладки на его поверхность не было водоотделения. При отделке цветными поризованными растворами с цветными каменными материалами и без них, с последующим вскрытием фактуры, на дно формы рекомендуется вносить саморазрушающийся клей или составы, ослабляющие прочность цементной пленки. Например, песок, смоченный 5-10% раствором декстринового клея до влажности 6-8% и др.
4.7. Отделка каменными дроблеными материалами выполняется путем укладки дробленого материала (гранит, мрамор, стекло и др.) фракции 10-20, 20-40 мм (расход до 15 кг/м2) на клеевое саморазрушающееся покрытие или на слоя песка влажностью 6-8 %, или на слоя песка с гипсом в соотношении 4 : 1 (по массе). Толщина подстилающих слоев, уложенных на дно формы, должна быть меньше крупности дробленого материала примерно в 2 раза.
4.8. Применение дробленых каменных материалов фракции 25-40 мм допускается с учетом соблюдения требований к толщине защитного слоя ячеистобетонного изделия или по согласованию с проектной организацией.
4.9. Уложенные на постилающий слой каменные дробленые материалы утрамбовывают.
4.10. При отделки панелей из виброгазобетона с целью предотвращения смещения каменных дробленых материалов при вибрации, на их поверхность после укладки распылителем наносят пленкообразующие полимерные материалы СКС-65ГП, МБМ-5с, разведенные водой до 15-25 %-ой концентрации. Установку каркасов и заливку ячеистой смеси с применением гасителя струи производят не ранее, чем через 1,5 часа после нанесения латексного покрытия. Примерный расход латекса - 0,2 л на 1 см .
4.11. Отчистку панелей от подстилающего слоя песка производят металлическими щетками после распалубки панелей.
4.12. Комбинацией разных по цвету и фактуре дробленых материалов можно получать на поверхности изделий цветные орнаменты и рисунки, выполняемые с помощью специальных шаблонов из круглой профилированной стали. При отделке щебнем мелкой фракции шаблон устанавливают в форму до укладки дробленых материалов. При изготовлении изделий с орнаментом из щебня крупного размера шаблон устанавливают в форму после укладки подстилающего слоя. После укладки дробленых материалов шаблон убирают.
4.13. Отделка коврово-мозаичной стеклянной, керамической и плиткой «брекчия» выполняется укладкой на дно формы ковров из керамической или стеклянной плитки с последующей укладкой промежуточного слоя из поризованного раствора (при литьевом способе формования) или газобетонной смесью (при вибрационном способе формования). Ковры в форме укрупняются с соблюдением требуемого размера швов между плитками.
4.14. В отдельных случаях допускается изготавливать ковры не предприятиях ячеистого бетона. Клей для наклейки плиток на бумагу и укрупнения ковров в формах должен удовлетворять требованиям СН 389-68 «Указания по заводской отделке керамической плиткой железобетонных и бетонных наружных стеновых панелей и блоков». Он должен легко смываться, обеспечивать необходимую прочность сцепления плитки с бумагой, не загрязнять и не менять цвета фасадной поверхности панелей.
4.15. Ковры раскладывают на дно формы так, чтобы крайние ряды плиток находились на расстоянии 2,5 см от борта формы или подходили к фаске. Поверхность уложенных ковров должна быть чистой и сухой. При отделке торца панели ковер наклеивают на борт формы с одновременным перегибом и приклеиванием его нижней части ко дну формы, а верхний - к горизонтальной плоскости борта. Фаски на панелях не отделывают.
4.16. Время вибрации ячеистобетонной смеси не должно превышать 5 мин, в противном случае возможно ослабление прочности сцепления плиток с ячеистым бетоном.
4.17. После распалубки изделий с их поверхности необходимо сразу удалить бумагу, затем поверхность панели дополнительно отчистить металлическими щетками и промыть водой. 4.18. Рельефную поверхность ячеистого бетона или поризованного раствора получают с помощью стальных, асбестовых, бетонных матриц или других рельефообразующих материалов, укладываемых на дно формы. Угол наклона граней рельефа матриц должен быть не менее 600, а глубина западающего рельефа должна составлять не более 10% толщины панели. На рельефную поверхность после распалубки следует нанести защитно-отделочное, либо гидрофобное покрытие. 4.19. Рельефообразующие материалы (щебень, арматурная сетка, металлические стержни, цильпебс и т. п.) размещают по дну формы произвольно или по заданному рисунку и закрывают предварительно пропитанным смазкой мягким рулонным материалом или синтетической пленкой, которую защемляют бортами формы. Металлические материалы можно приварить ко дну формы, а неметаллические -прикрепить эпоксидным клеем ЭПЦ-1 ил ЭПЦ-2.
4.20. Окончательную обработку наружной поверхности изделий производят после их распалубки. Для удаления масляных пятен, клея, бумаги, неприставших дробленых каменных материалов, для вскрытия фактуры, снятия цементной пленки с поризованных растворов применяют мозаично-шлифовальную машину С-475 или С-420. Для получения мелкозернистой поверхности - пескоструйный аппарат, универсальную машину УМ-205, машину ОЛ-107Д со сменными механизмами или грунтовочно - зачистную машину конструкции НИПИсиликатобетон. Для получения рельефа в виде борозд применяют машины с различными по форме фрезами.
5. Технология отделки, осуществляемой после распалубки панелей в заводских условиях.
5.1. Отделка поверхностей панелей после их распалубки осуществляется следующими двумя способами:
а) окрасочными составами (водоэмульсионными, органическими, цементными, эмалевыми и гидрофобными красками), а также декоративными тонкослойными растворами (см. пп. 5.9 - 5.29);
б) мелкозернистыми цветными декоративными присыпками, которые наносятся на панели по специальному клеящему основанию (см. пп. 5.30 - 5.34).
5.2. Независимо от вида отделки, осуществляемой после распалубки, на поверхностях панелей не допускается:
а) раковины глубиной более 2 мм, диаметром не более 3 мм;
б) трещины в бетоне шириной не более 0,2 мм;
в) местные наплывы, впадины глубиной более 2 мм и диаметром более 5 мм, «драконов зуб» высотой более 1,5 мм;
г) газобетонная пыль;
д) масляные пятна;
е)отслоения поверхностей цементной или известковой пленки.
При наличии дефектов их рекомендуется устранить, произвести, при необходимости, ремонт и подготовить поверхность панелей под отделку.
5.3. Подготовка поверхности изделий под отделку включает:
а) отчистку поверхности от масляных, ржавых пятен, грязи и отслоившейся цементной или известковой пленки (п. 5.4.) с последующим обеспыливанием поверхности;
б) заделку раствором отдельных выбоин, обколов граней, ребер и мелких трещин (п. 5.5.);
в) выравнивание поверхности раствором (п. 5.6., табл. 5);
г) огрунтовку поверхности латексом СКС-65 ГП, разведенным водой в соотношении 1:3 (латекс : вода).
5.4. Отчистку поверхностей изделий от масляных пятен и грязи производят абразивными инструментами, металлическими щетками, пескоструйным аппаратом, либо грунтовочно - зачистной машиной. Зачищенные поверхности продувают сжатым воздухом или обеспыливают с помощью пылесоса.
5.5. Ремонт выбоин и обколов ребер, углов, граней рекомендуется производить ремонтным раствором состава: цемент : известь : песок - 1 : 0,2 : 4 (масс. ч.) с добавлением 10% дисперсии ПВА 50%-й массы цемента. Вода вводится в количестве, необходимом для получения раствора консистенции 8-10см по конусу СтройЦНИЛа. При больших отколах углов и ребер растворы следует наносить по металлической сетке (тканью № 12 с диаметром проволоки 1,2 мм) или оцинкованной проволоке диаметром 1,5-3 мм, закрепленных оцинкованными гвоздями (гвозди круглые с конической головкой и гвозди трефовые с перемычкой, ГОСТ 4028-63 с изм., длиной 200мм, диаметром 6 мм, имеющие антикоррозийную защиту).
5.6.Последовательность ремонтных операций следующая:
а) отчистка изделий от разрушенного бетона;
б) на участке, подлежащем ремонту, в бетон в шахматном порядке под углом 75-800 вбиваются гвозди на глубину не менее 100 мм;
в) на гвозди надевается полотно металлической сетки, вырезанное по размеру ремонтируемого участка, и закрепляется оцинкованной проволокой;
г) поверхность ячеистого бетона смачивается водой и затем наносится раствор. Устранение крупных дефектов и выравнивание поверхностей изделий производят ремонтными растворами.
5.7. Компоненты раствора для заделки дефектов перемешивают в смесители в следующей последовательности: половинное количество воды перемешивают с ПВАД (или СКС-65 ГП, СКС-65 ГПБ, МБМ-5с) 2-3 мин. Затем вводят песок, портландцемент или смесь цементов, или измельченный газобетон, остальную воду и полученную смесь перемешивают еще 4-6 мин. Пластичность раствора должна быть 8-10 см по конусу СтройЦНИЛа.
5.8. Ремонтные растворы наносят на поверхность панелей, предварительно покрытых водным раствором поливинилацетатной дисперсии (ПВАД), либо латекса СКС-65 ГП или эмульсии МБМ-5с. Соотношение полимера и воды 1:3 (по объему).
5.9. При отделке окрасочными составами и декоративными тонкослойными растворами на поверхность панелей наносят следующие три слоя: грунтовочный, шпаклевочный и отделочный, который является заключительным покрытием всей отделки. Характеристики этих слоев для всех видов окрасочных составов.
5.10. Нанесение покрытий на основе лакокрасочных материалов рекомендуется производить на механизированных конвейерных линиях (п. 5.12.) или на стационарных постах. При нанесении лакокрасочных материалов на органических растворителях влажность ячеистого бетона в поверхностном слое на глубине 5 мм не должна превышать 8% (по массе), при нанесении водоэмульсионных красок и полимерцементных составов влажность ячеистого бетона не регламентируется. Конвейерная линия или стационарные посты для отделки размещаются в отапливаемых помещениях. Здесь же размешаются краско - заготовительное отделение и кладовая для хранения суточного запаса рабочих составов и декоративных материалов.
5.11.Приготовление грунтовочных, шпаклевочных, клеевых и окрасочных составов (смесей) производят в смесителях СБ-43, С-716, С-365, СО-11, С-411А, акустическом быстроходном смесителе АУРК и др. Составы на растворителях приготавливают или разводят в плотно закрытых смесителях или красконагнетательных бочках С-362, С-764. Составы должны быть однородны, не иметь сгустков, комков и загрязнений.
5.12. На конвейерной линии отделки с вертикальным расположением панелей (конструкции НИИЖБ, НПО Лакокраскопокрытие, КБ по железобетону) грунтовочные, шпаклевочные или клеевые составы, декоративные присыпки и отделочные составы наносят электростатическими лотковыми или пневмоэлектростатическими распылителями РВПЭ. На конвейерных линиях с горизонтальным положением панелей с помощью машин для заводской отделки и с помощью механических устройств, оснащенных специальными бункерами с затвором, обеспечивающим равномерное распределение составов (конструкции ВНИИстроммаш, ВНИИстром).
5.13. На стационарных постах грунтовочные и отделочные составы наносят с помощью краскораспылителей КРВ-2, пистолетов - распылителей С-45, С-592, СО-19а, СО-71 и др., соединенных с красконагнетательным бачком С-411 или пистолетом ГСХ (Р-68), установки С-562. Шпаклевочные составы с цементом, молотым песком или крупным наполнителем наносят с помощью пистолета ГСХ (Р-68), установки С-562, растворонасос с форсункой ФК-1 или других устройств, распыляющих вязкие составы с наполнителем. Декоративные присыпки наносят пневматическим распылителем «Крошкомет» или электростатическим лотковым распылителем «Декостат».
5.14. Грунтовочные, шпаклевочные и отделочные слои (покрытия) наносят равномерно по всей поверхности. При этом каждая следующая полоса покрытия должна перекрывать ранее нанесенную на 3-4 см.
5.15. Краски ЭКЧ-112 и латексы СКС-65ГП, СКС-60ГП поступают с лакокрасочных заводов в готовом виде, до требуемой консистенции разводятся водой. Для приготовления шпаклевочных составов краску тщательно перемешивают с цементом или молотым песком (40 % массы краски) в течение 15-20 минут в смесителях принудительного действия, готовая шпаклевка должна представлять собой однородную смесь без сгустков, комков, не коагулировать в течение 3 часов. Для предотвращения коагуляции краски при введение цемента в ее состав вводят 10-15 % стабилизатора ОП-7 или раствора казеина аммония; 25%-й раствор казеина аммония состоит из смеси казеина и воды, взятых в соотношении 1:4 (по массе) и раствора аммиака (20 мл на 1 кг казеина) в количестве 10%. Для получения отделочного состава краску исходной вязкости разбавляют водой и перемешивают в быстроходном смесителе до однородной консистенции. Для получения покрытий с шероховатой фактурой в краску вводят песок или крошку горных пород фракцией до 1,5 мм в соотношении 1:2 (мас. ч.).
5.16. краски Э-ВА-17 и дисперсия ПВА 50%-я поступают с лакокрасочных заводов в готовом виде, до рабочей вязкости разводятся водой. Шпаклевочный состав приготавливают в смесителях путем введения краски Э-ВА-17 (вязкостью 60 с по ВЗ-4) с добавлением жидкости 136-41 (0,1-0,2% массы краски) и цемента или молотого песка (40% массы краски) и перемешивают состав в течение 10-20 минут до получения однородной смеси. Краску для отделочного слоя приготавливают в быстроходных смесителях; допускается приготовление ее обычных смесителях, но при этом необходимо ее процеживать. Для получения шероховатой поверхности в краску вводят песок или крошку горных пород с размером зерен до 1,5 мм в соотношении краска : наполнитель= 1:2 (мас. ч.).
5.17. Латексно - цементные краски приготавливают на предприятиях ячеистого бетона в краскозаготовительном отделении путем перемешивания следующих компонентов (%): латекс СКС-65ГП-30,6, 25%-го раствора КМЦ-1,3%, 50%-го раствора ОП-7-1,8, калиевого жидкого стекла (плотностью 1,27) - 1,8, жидкости ГКЖ-11 - 1 и сухой смеси - 64,5. краски разводят водой. Срок годности краски 3-4 ч.
КОМПОНЕНТЫ СОСТАВ, % ПО МАССЕ
Портландцемент белый 15
Песок крупностью не более 0,5 мм и влажностью до 1% 18,4
Сухая газобетонная пыль 30,6
Пигменты (по колеру) -
Полимерное связующее приготавливают в смесителях путем перемешивания последовательно вводимых а латекс СКС-65ГП добавок ОП-7, КМЦ и жидкого стекла. Предварительно ОП-7 и КМЦ смешивают с водой, первый в соотношении 1:2, второй -1:3 (по массе) и выдерживают 24 ч. В полимерное связующее при перемешивании небольшими порциями вводят сухую смесь, а затем жидкость ГКЖ-11. Готовая краска процеживается через сито с отверстиями диаметром 1,5 мм.
5.18. Краски ПВАЦ и ПВАГ приготавливают на предприятиях ячеистого бетона путем перемешивания поливинилацетатной дисперсии ПВА 50%-й, цемента или измельченного газобетона, кремнефтористого натрия, пигментов, песка и воды (табл. 8). срок годности краски 3ч. Краску можно наносить при температуре воздуха не ниже минус 50С. Сухую смесь краски приготавливаю отдельно путем тщательного перемешивания в вибро- или шаровых мельницах компонентов до тонкости помола, характеризующейся остатком на сите 0085 не более 3%. При приготовлении краски в смеситель сначала заливают воду (40-50% общего количества при приготовлении шпаклевочного состава и 60-70% окрасочного) и дисперсию ПВА. После 2-3 минут перемешивания добавляют оставшуюся воду и перемешивают еще 4-6 минут. Для получения шероховатой фактуры в краску вводят песок или крошку горных пород с размером зерен до 2 мм в соотношении краска : наполнитель 1:2 (мас. ч.). После нанесения на изделие отделочного покрытия изделие рекомендуется выдерживать в течение суток при температуре воздуха 15-18 0С.
#При приготовлении краски ПВАЦ целесообразно применять дисперсию ПВА непластифицированную (Д 50С) или малопластифицированную (ДФ 48/5с), а пластификатор- дибутилфталат вводить в цемент в количестве 5% (при использовании непластифицированной ПВАД) или 4% (при использовании малопластифицированной ПВАД) его массы. Это приводит к повышению жизнеспособности состава и трещиностойкости ПВАЦ покрытия.
5.19. Цементные краски приготавливаются на предприятиях ячеистого бетона петем перемешивания сухих компонентов с водой (40-70% массы сухих компонентов) и дисперсией ПВА 50%-й пластифицированной. Состав краски дан в табл. 9. Для приготовления шпаклевочного состава в краску вводят песок крупностью до 2 мм в количестве 20% по массе от сухой смеси краски.
5.20.Фосфогипсополимерный состав «Полифос» представляет собой смесь (мас. ч.) : фосфогипса 30%-й влажности - 1, дисперсии пластифицированной ПВА 50%-й - 0,35, воды - 0,3-0,5, наполнителей и пигментов - 0,25. Содержание воды зависит от влажности фосфогипса.
Примечание. В сухие смеси краски, предназначенные для длительного хранения, хлористый кальций не вводят. Его добавляют в воду затворения при приготовлении краски. Состав приготавливается на предприятиях ячеистого бетона в смесителе при последующей загрузки материалов: вначале дисперсию ПВА перемешивают с частью воды и фосфогипсом (50%) в течение 2-3 минут, затем вводят фосфогипс и оставшееся количество воды, а также наполнители и пигменты и перемешивают в течение 8-10 минут до получения однородной массы. Готовый состав процеживают через сетку диаметром отверстий 1,25 мм. Жизнеспособность готового состава при хранение в закрытых емкостях - 1 год. шероховатую фактуру поверхности получают путем введения в состав декоративной крошки (гранита, мрамора, пластмассы, отходы тонкой керамики, кирпича, черепицы, стекла) в отношении 1:1 (состав : наполнитель) или нанесение ее на отделочный слой с помощью «Крошкомета». При отделки горизонтальных поверхностей можно использовать крошку фракцией 1-5 мм и 1-2,5 мм - при отделки вертикальных поверхностей изделий. Состав наносится пистолетом - распылителем ГСХ (Р-68), СО-24А и др. Толщина отделочного слоя 1,5-2 мм, с фактурой 2-3 мм. Для получения цвета в состав рекомендуется вводить пигменты либо цветной цемент.
5.21. Составы «Полигран» готовят на заводах ячеистого бетона путем перемешивания в смесителе латекса СКС-65ГП, раствора казеинового клея и гранулята в соотношении, указанном в табл. 10. Приготовление раствора казеинового клея сводится к затворению порошка клея водой комнатной температуры в соотношении 1:4 (клей : вода) по массе. Время набухания -1 час. Приготовление полимерминерального состава «Полигран» осуществляется в смесителях при следующей загрузки материалов: латекс СКС-65ГП «Б», 4%-й водный раствор универсального стирального порошка, кремнийорганическая жидкость, казеиновый клей, гранулят. Смесь перемешивают в течение 8-10 минут. Жизнеспособность состава в закрытой таре - 6 месяцев, расход 2-3 кг/м2, время сушки покрытия от 4 до 24 часов в зависимости от температуры окружающей среды (+5-25 0С). Нанесение отделочного состава производится пистолетом или агрегатом, распыляющим вязкие отделочные составы при давлении воздуха 0,4-0,6 МПа.
5.22. Отделку цементно-перхлорвиниловыми красками ЦПХВ выполняют в камерах или на постах, оборудованных приточно-вытяжной вентиляцией, либо в построечных условиях.
Краски ЦПХВ наносят в два слоя с промежуточной пропиткой шпаклевочного слоя 5%-м перхлорвиниловым лаком, вязкостью 5 с по ВЗ-4. На предприятиях ячеистого бетона краски ЦПХВ поступают в готовом виде в герметической таре, и должны хранится в специальных помещениях с соблюдением противопожарных и санитарных требований. Разбавление красок до рабочей вязкости производят ксилолом при медленном перемешивании в небольших емкостях и специальных помещениях, оборудованных приточно-вытяжной вентиляцией, до разбавления краски необходимо тщательно размешать. Краски наносят кистью, валиком, пистолетом - распылителем ГСХ (РВ-68), СО-41 и др., при температуре воздуха не ниже 50С.
5.23. Отделку эмалью ХП-71 фвыполняют в камерах или на постах, оборудованных приточно-вытяжной вентиляцией. Эмали ХП-71 ф и ХП-71 ф марки К, а также лак ХП-071ф поступают на предприятия ячеистого бетона в готовом виде в герметической таре, должны храниться в специальных помещениях с соблюдением противопожарных и санитарных требований. Срок годности составов 6 мес. Краски разбавляют до рабочей вязкости ксилолом, толуолом или сольвентом в специальных помещениях, оборудованных приточно-вытяжной вентиляцией. Наносятся эмали в 2-3 слоя кистью, валиком или пистолетом -распылителем ГСХ (РВ-68), СО-21 А и др. при температуре 18-20 0С. Перед употреблением краски следует перемешать до полной однородности.
5.24. Отделку органосиликатными красками ОМС ВН-30ДТС производят в два слоя в окрасочных камерах или на постах, оборудованных приточно-вытяжной вентиляцией. Краски ОМС ВН-30 поступают в готовом виде и должны хранится в специальных помещениях с соблюдением противопожарных и санитарных требований. Краска до рабочей вязкости разводится толуолом. Перед нанесением в краску добавляют отвердитель ТБТ или ПБ-1 в количестве 1-2% (по сухому остатку). Срок годности краски ОМС ВН-30 ДТС не более года с момента изготовления. Грунтовочный и окрасочный состав рекомендуется наносить писталетами -распылителями СО-24, СО-71 с красконагнетательным бочком ГСХ (Р-68). Краски перед употреблением следует перемешивать до полной однородности. Сжатый воздух, подаваемый в красконагнетательный бачок, должен отчищаться в масловодоотделителе.
Источник: ПП Будпостач